Table of Contents
Low-temperature-curable powder coatings are often touted as the next generation of coating technology due to their environmentally inoffensive list of ingredients, energy-saving cure requirements, and ability to coat a variety of substrates that cannot withstand typical powder coating curing processes. However, the processes by which powder coatings are produced impose limitations on how low we can ultimately drive the cure temperatures. Standard powder coatings are typically cured for 10-20 minutes at temperatures ranging from 160-200°C.
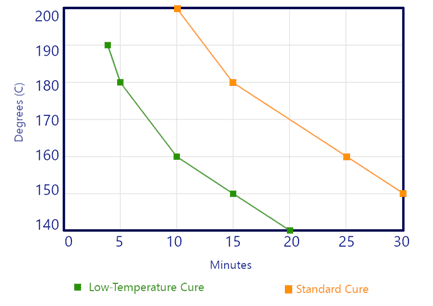
(Source: ChemQuest Powder Coating Research)
The heart of the powder coating manufacturing process is the extruder. Solid resins and crosslinkers, colorant pigments, mineral fillers, and additives are first dry-mixed and then introduced to the extruder. The mechanical shearing force of the rotating screws in the extruder deagglomerates pigment particles and non-melting particles.
The extruder barrel is set at a temperature in the 90-115°C range, high enough that the polymeric components can be melted and intimately mixed. The dwell time in the extruder is kept to a minimum, and the homogenous mixture is discharged from the barrel and cooled to prevent any pre-reaction of the thermosetting materials.
Therein lies the low temperature conundrum. Processing at 100°C leaves a safe working margin for coating designed to cure at 160-200°C. As the cure temperature drops, the gap becomes smaller and the risk of prematurely reacting in the compounding process gets larger. Ultimately, a powder coating formulation could be devised with a cure temperature significantly lower than those currently in production – but it could not be safely manufactured using traditional equipment and practices.
Over the years, clever technologists have devised different approaches to powder coating production, but the extruder is a long way away from being dethroned as the preferred method of compounding. High-intensity mixing does not provide nearly the degree of mixing that is possible with an extruder, and the benefits of using a high-throughput continuous process would be lost. Ultrasonics can aid in the deagglomeration of fine particles but fall short in blending resinous materials. Other approaches like the use of heated pressure plates may be viable in a lab but are not realistic for production at scale.
Latent Catalysts and Blocking Agents
One potential solution could involve the development of latent catalysts and blocking agents from raw material suppliers. An example would be the way isocyanate crosslinkers are designed for the current powder coating market. Free isocyanates are far too reactive to undergo the extrusion process, so they are capped with a sacrificial blocking agent that is released when the coating reaches a designated temperature.
The most common of these is ε-caprolactam, which is released at around 170°C, making it safe to extrude while offering excellent storage stability. Alternative blocking agents have been used to decrease the unblocking temperature, including triazole (140°C) and pyrazole (150°C). Triazole has an unfavorable toxicity profile, being classified as a teratogen, and pyrazole is expensive, affecting its commercial practicality. Isocyanates may also be internally blocked, such as with the use of an unstable uretdione ring. The bond is cleaved around 160°C, though work has been done using unique catalysts to reduce the unblocking temperature to around 130°C.
Latent catalysts could work on a similar principle for other powder coating chemistries. Latency could be built in utilizing a blocking agent or encapsulation technology, allowing for processing under ideal conditions and triggering as soon as the target cure temperature was met.
Two-Part Systems
Liquid coatings have long eluded problems pertaining to early reactions by splitting the reactive species into two components, often referred to as a 2K system. In liquid paints, the two components are mixed at the point of application right before being sprayed onto the part.
In a powder coating environment, a producer could manufacture an A batch of powder containing the primary resin and a B batch containing the crosslinker and catalyst, then blend them together in their powdered form. One drawback of this approach is the added cost of manufacturing two batches and post-blending. The other is that powder coatings have limited molecular mobility in their molten state and may be physically hindered to effectively form a robust polymeric network. Research in this area is ongoing, and commercial options may be on the horizon.
Alternative Curing Methods
Finally, the issue may be solved by decoupling the melt/flow process from the curing stage. With traditional thermosetting powder coatings, parts are coated electrostatically and exposed to a designated time and temperature in a curing oven. The solid particles first melt and flow, resulting in the desired surface structure and appearance before the reactive components of the formula begin to crosslink and build molecular weight.
Radiation-cured powder coatings take a different approach to this process. Crosslinking does not occur until the coating is exposed to an ultraviolet or electron beam radiation source that is matched to the photoinitiator or, alternatively, to a photoacid generator formulated into the coating. As a result, the film forming stage can be undertaken using any combination of convection and/or infrared heating before being presented to the curing stage. This also eliminates the possibility of pre-reaction in the extruder.
The downsides of UV-cure powder coatings include the limited range of formulations available, the line-of-sight nature of the curing mechanism, and the need for specialized curing equipment. That said, formulations are commercially viable for many applications where thermoset powders are not able to be used.
Developing Opportunities
The next big leap in technology for low-temperature-cure powder coatings could come from new manufacturing processes, innovative heat-activated chemistry, or advanced application and curing methods. Whatever the breakthrough, commercializing these truly next-generation products will provide the potential to coat temperature-sensitive substrates with a high-quality, environmentally friendly, and energy-efficient finish.
For more information, reach out to the author at nbiller@chemquest.com or visit https://chemquest.com/cqpcr.
Read in PCI.