Operational Excellence
Improve End-to-End Operations and Efficiency
How can you identify, implement, and sustain improvements that lead to profitable growth?
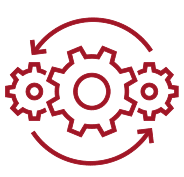
Are your systems and processes operating at optimal levels?
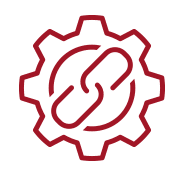
Can your supply chain performance be improved?
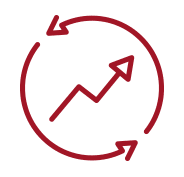
Are you able to improve quality performance results over time?
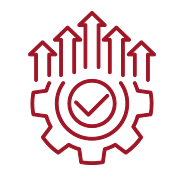
Are you considering reshoring, expansion, or relocation of your current facility?
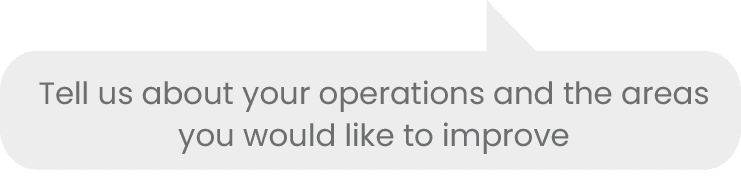

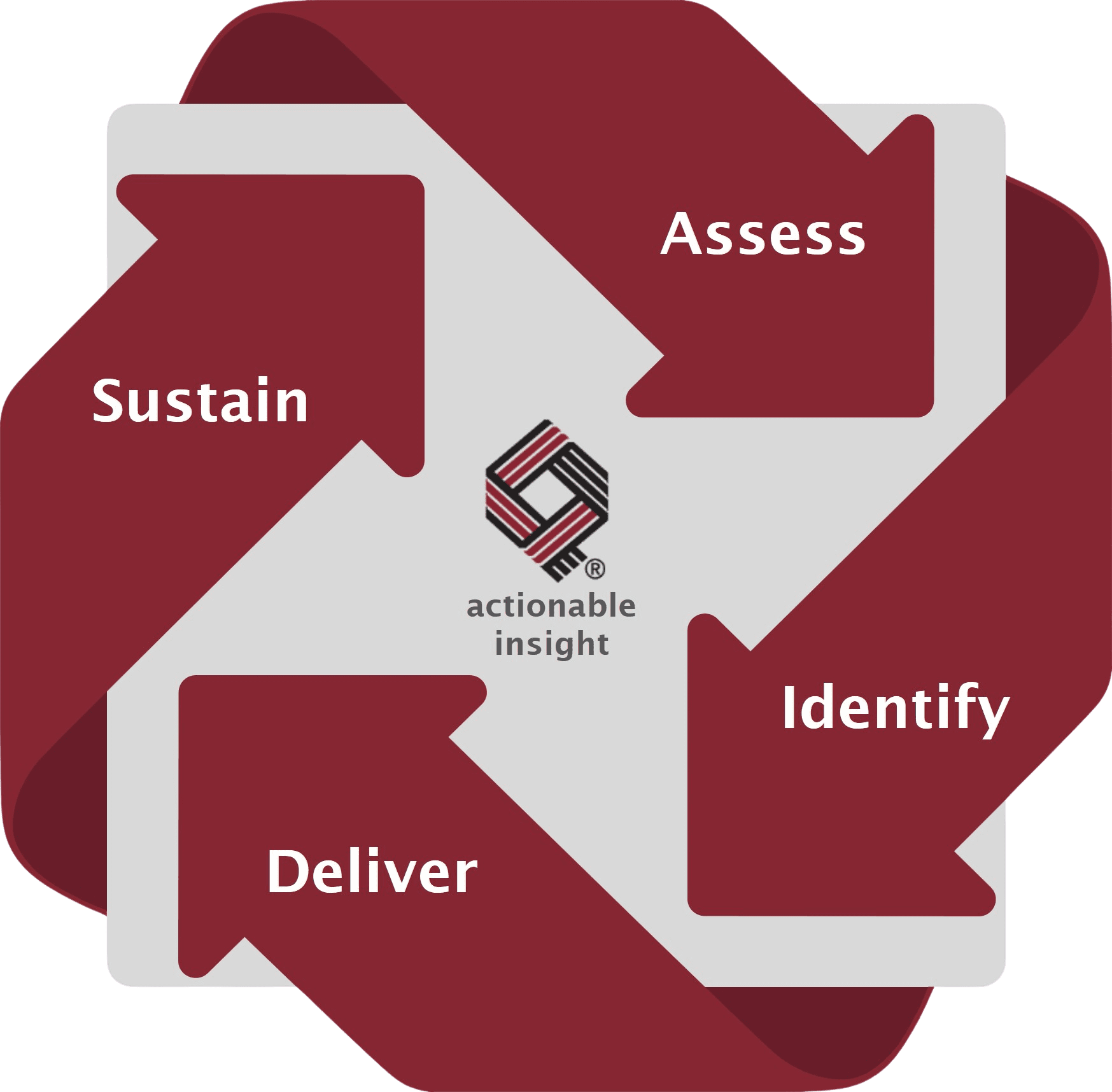
Our Operational Excellence Process
It starts with a conversation, protected by a Non-Disclosure Agreement, and leads to a personalized proposal to meet the objectives we jointly identify.
Our holistic and collaborative approach identifies gaps, builds capabilities, delivers on efficiencies, and sustains value for your long-term success.
Assess
Conduct an end-to-end assessment of your entire operation
READ MORE
We will assess your operations from end to end, culminating in a scorecard for each value stream/department.
Action steps include:
- Site walk-through to develop a site flow assessment
- Review current state (quality, KPIs, financials, SKUs, pricing)
- Safety overview
- Technical assessment
- Interviews with leadership
- Problem identification/clarification
- 1-2 days per site
Identify
Analyze uncovered gaps and provide a corrective plan
READ MORE
Our team will use the knowledge gathered in the Assess process to analyze gaps and develop a corrective plan.
You’ll receive:
- Implementation plan and schedule
- Highlights of quick wins/fixes
- Review of needed modalities to make the change and how working a few of them together will get the win
Deliver
Turn insights into value by implementing the corrective plan
READ MORE
Now we help you turn these insights into value.
We’ll support you by:
- Showing you how to implement the corrective plan developed in the Identify phase
- Becoming part of your team to build capabilities
- Providing operational strategy education (classroom-type learning)
- Providing on-the-line coaching (KPI tracking, best practices for our Operational Excellence system)
- Scheduling regular visits (monthly/biweekly/on-site or virtual)
Sustain
Provide coaching and guidance to ensure the implementation value is sustained and institutionalized as part of change culture
READ MORE
We work with you on team development to ensure the value is sustained for the future.
You’ll receive our team’s ongoing insight and support through:
- Solution Scorecard report, which provides insights and plan for corrective action
- KPI tracking
- Safety overview
- Coaching, guidance, counsel
- Maturity Scorecard review – competency (updated view of same scorecard from the Assess phase)
- Accountability partnership
- Scheduled quarterly visits to suit your needs
We have a Playbook for all your Operational Areas
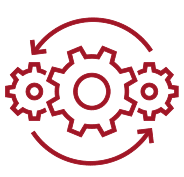
Process Optimization
- Lean methodologies
- Change management
- Quality management
- Alternate technologies
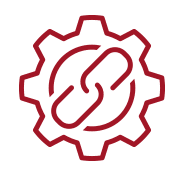
Supply Chain
- Relocation or reshoring
- Inventory management
- Mitigate supplier dependency
- Mitigate tariffs
- S&OP (sales and operations planning)
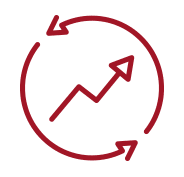
Capacity & Production
- Increased yields
- SKU management
- S&OP (sales and operations planning)
- Asset management
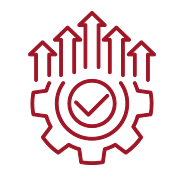
Expansion Planning
- Growth options
- Risk mitigation
- Capex investment strategy
- Factory design

Environmental Health & Safety
- Best practices and compliance
- Reporting frameworks
- Training support
Our Results
KPI improvements lead directly to EBITDA gains.
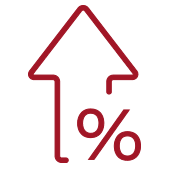
Improved Production Rate/OEE
Typical improvement: 5-30%
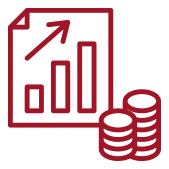
Yield/Quality Improvement
Typical improvement: 2-20%
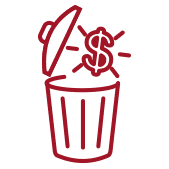
Reduction of Processing/Waste Costs
Typical improvement: 5-30%
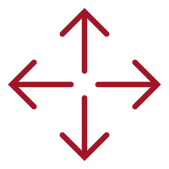
Alternate Processing Options
Typical improvement: 20-40%
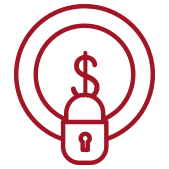
Optimized Fixed Costs
Typical improvement: 5-15%
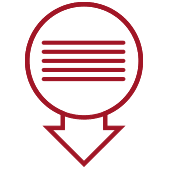
Reduced Inventory
Typical improvement: 20-30%
Operational Excellence Success Stories
Learn more about ChemQuest
Enter your email address to download our Introduction to ChemQuest PDF