The concepts of viscosity and rheology are often confused, even though they are significantly different. For this discussion, rheology is the study of the flow and deformation of liquids (paints and varnishes) under applied forces. Rheology includes viscosity, elasticity, and plasticity. Viscosity, on the other hand, is defined specifically as a measure of resistance to deformation under shear stress and is the most common rheological measurement of a paint system. Viscosity is often likened to the “thickness” of a fluid. In short, rheology is the broad study of how materials flow and deform, while viscosity is a more specific property related to a resistance to flow.
Viscosity is one of the defining properties of commercial paint systems and is always listed on a technical data sheet to ensure quality control and performance. Viscosity can be calculated but is generally best measured directly. Equipment ranges from the simple Ford Cup, which measures one flow time at a single rate, to the digitized viscometers that are set up to measure a variety of flow rates quickly.
When measuring viscosity, it is important to understand whether the fluid is Newtonian or non-Newtonian. The viscosity of Newtonian systems is constant and independent of shear rate. Non-Newtonian fluid viscosity is dependent on shear rate and changes accordingly. Paints, inks, and varnishes usually fall into the non-Newtonian category, while oils and lubricants tend to be Newtonian.
For example, one non-Newtonian behavior is shear thinning, where the liquid becomes less viscous when shear (mixing) is applied, as occurs during application. When the shear is removed, the liquid regains viscosity. This is a desirable attribute for many paint applications so that the paint can be easily applied but then does not drip or sag after application.
There are nine ASTM standards commonly used for measuring the viscosity of paint systems. Each standard measures viscosity at the point of approximating the paint application process. The standards are governed by two subcommittees in ASTM Committee D01 on Paint and Related Coatings, Materials and Applications. The most widely used standards include:
- ASTM D1200 Standard Test Method for Viscosity by Ford Viscosity Cup
- ASTM D1823 Standard Test Method for Apparent Viscosity of Plastisols and Organosols at High Shear Rates by Extrusion Viscometer
- ASTM D1824 Standard Test Method for Apparent Viscosity of Plastisols and Organosols at Low Shear Rates
- ASTM D2196 Standard Test Methods for Rheological Properties of Non-Newtonian Materials by Rotational Viscometer
- ASTM D4212 Standard Test Method for Viscosity by Dip-Type Viscosity Cups
- ASTM D4287 Standard Test Method for High-Shear Viscosity Using a Cone/Plate Viscometer
- ASTM D5478 Standard Test Methods for Viscosity of Materials by a Falling Needle Viscometer
- ASTM D7395 Standard Test Method for Cone/Plate Viscosity at a 500 s-1 Shear Rate
- ASTM D7867 Standard Test Methods for Measurement of the Rotational Viscosity of Paints, Inks and Related Liquid Materials as a Function of Temperature
With the variety of viscosity measurement standards available, it is possible to select techniques to determine viscosity parameters for product families, application methods, or overall behavior at different temperatures and/or shear rates. Table 1 provides a guide to the type of viscosity measurements governed by each standard, along with the significance of those measurements to application parameters or to viscosity behavior at various temperatures or shear rates.
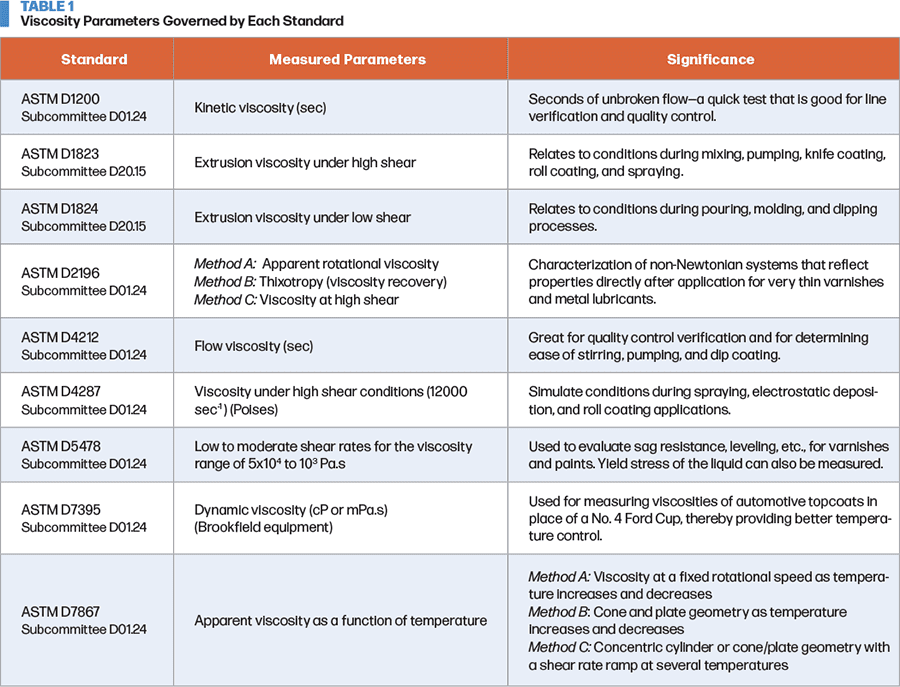
ASTM viscosity testing can be used to analyze either general paint characteristics or fluid conditions at certain steps in the painting process. The variety of tests available ensure that viscosity parameters can be measured as a simple quality control operation or as a defining characteristic of the paint system. Using the correct test enhances the quality of the overall process.
To learn more, reach out to the author at cgosselin@chemquest.com.
Read in CoatingsTech.