Table of Contents
Most ASTM standards describe testing methods and protocols for analyzing individual material characteristics. There is also a group of standards that provide broad information needed for specific products. Those standards consolidate the variety of testing methods needed to ensure that a product system exhibits the required characteristics, attributes, and longevity in field service.
One such standard is ASTM A755/A755M Standard Specification for Sheet Steel, Metallic Coated by the Hot-Dip Process and Prepainted by the Coil-Coating Process for Exterior Exposed Building Products. This standard is used successfully around the world, as prepainted building panels are a huge percentage of coil-coated products. Further, enhancements to this standard have been provided by a variety of international ASTM members, making it a comprehensive guide for building panel products.
Details Included in the Product Specification
First developed in 1978, this standard was updated every five years through 2024 to define and describe the requirements for the metal substrates and organic coatings utilized for exterior building panels. In addition, mandatory and non-mandatory requirements for physical and mechanical tests performed during production are included to assist in obtaining a fully functional exterior building-panel system. Another benefit of product specifications is that the relevant material specifications and testing methods are routinely updated, removed, or added during the five-year review process as the technology moves forward.
This specification covers all aspects of the building panel system. The metallic-coated sheet steel substrates are defined through listed referenced ASTM standards governing the base metal chemistry, formability grades, and metallic-coating weights, and chemistries.
The applicable organic coatings are also listed and defined. Terms such as acrylic, polyester, fluorocarbon, plastisol, polyurethane, and silicone polyester are identified as potential topcoats. The need for conversion coatings applied prior to coil coating is highlighted to provide an adhesion promoting surface suitable for painting and in-service durability.
Required organic coating aesthetic characteristics such as chalking, fade, and gloss are explained and listed in the standard because they are the most visible attributes. In addition, explanations are provided for the need for primers, topcoats, washcoats and backer systems. Typical film thickness requirements for the organic systems are included to ensure durability, corrosion resistance, and aesthetics in a wide variety of service environments.
Manufacturing and ordering details are also included for the system. This includes minimum recommended coating weights for zinc, zinc-aluminum, aluminum, and zinc-aluminum-magnesium-alloy metallic coatings.
The application of organic coatings on a continuous coil coating line involves three major application steps: conversion coatings, primer, and topcoat(s) on the exposed side. At the same time, washcoats or backer coatings are applied on the unexposed side to provide additional corrosion resistance and lubricity for the panel forming process. Metallic and non-metallic coatings are tailored for use in proposed service environments and levels of system performance are usually agreed upon between the producer and purchaser, with coating specifics defined in product data sheets.
Proper storage of building panels prior to erection has been found to be important to maintaining the integrity and corrosion resistance of the coated system. Pallet storage is codified to ensure protection of panels and coils.
Testing Protocols
Finally, the ASTM methods for testing physical and mechanical properties of coil-coated building panel products at the time of production are included in a mandatory Annex. Those testing protocols are familiar to most coating manufacturers and users. Included in the Annex are the tests and standards in Table 1.
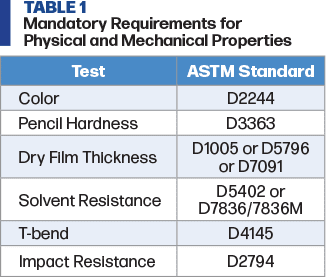
Table image courtesy of CoatingsTech.
There is also a non-mandatory Appendix that includes additional ASTM testing methods for the performance evaluation of coil coatings which may be desired, but not required during the manufacturing process. Again, those testing methods are familiar to most coating manufacturers and users and are listed in Table 2.
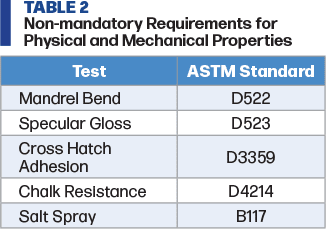
Table image courtesy of CoatingsTech.
Test methods used to predict the behavior of building panel products in field service are also included in the Appendix. The tests in Table 3 are usually conducted by paint companies, exposure testing laboratories, and (in some cases) purchasers during qualification.
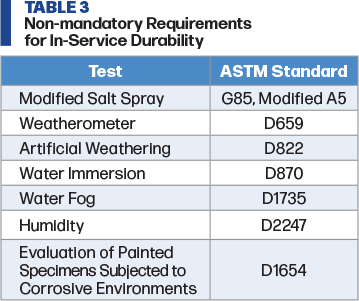
Table image courtesy of CoatingsTech.
ASTM standards that define, explain, and consolidate the various standards and necessary characteristics within product specifications provide a valuable resource when navigating the many aspects of successful in-service performance.
To learn more, reach out to the author at cgosselin@chemquest.com.
Read in CoatingsTech.