Table of Contents
“We have too many linear thinkers, but we live in a three-dimensional world.” –Eric M. McCracken
The specialty chemicals producers and their raw material suppliers, whether working in paints and coatings, adhesives and sealants, lubricants, personal care, or any other areas, could learn a lot from trophy-winning horse trainers. Why? Because elite horse trainers understand that there is no “straight line” in training a horse to perform what the rider asks of it—every horse is different and requires a unique approach to its training. Yes, certain aspects of training are going to be the same for all horses, so linear, data-driven thinking—“If I give the horse ‘signal X,’ the horse will perform ‘Maneuver Y’”—is a reasonable approach. Because horses have unique personalities, however, this type of training only works to a point, at which time one either gives up attempting to train the horse to perform a new maneuver, or one changes to less orthodox training approaches, trying many different and seemingly unrelated training exercises to see if any of them will connect with the horse’s understanding of the relationship between the rider’s request and the horse’s corresponding response. Many of these customized training techniques are learned from experiences with other horses in the past. This works, but it requires an approach that human observers tend to think of in terms of “non-linear thinking,” ”out-of-the-box thinking,” “lateral thinking,” and perhaps a few other terms. More to the point, it is the only way in which serious horse trainers can “predict the future” by “controlling the future” (i.e., by taking real-time actions in the present to maximize the chances for success in the future)—no trainer ends up with a winner in the Kentucky Derby without understanding the power of non-linear thinking applied to horse training.
And breeding trophy-winning horses is by no means the only activity in which predicting the future by controlling the future can be made a great deal more accurate and realistic by studying the past and, even more importantly, by studying what went wrong in the past, and why. Every successful business that wishes to remain successful moving into the future follows this approach as a matter of course. This is basically nothing more than “ISO 101,” but it’s shocking how often it is overlooked by middle managers who default to linear thinking because they have too much on their plate to take the time necessary to explore solutions to problems that do not involve straight-line approaches, and by upper-level managers who are fixated on the week-to-week, month-to-month P&L, which is strictly a linear activity, to be bothered by the strategic needs that must be put in place to enable their companies to exist in the future, much less flourish.
Scenarios like this are, of course, all too common and—while they are great for outside consultants like ChemQuest Group—they can wreak havoc within organizations that are paddling upstream without the slightest understanding of what they are doing, and why it is keeping them from making progress towards their goals.
The Great Supply Chain Crisis of 2021-2022 acted as a very loud and exceptionally clear wakeup call for all participants within the specialty chemicals value chain, whether in paints and coatings; sealants and adhesives; household, industrial & institutional cleaners (HI&I); lubricants and hydraulic fluids; personal care products; or many others. Its message was equally loud and clear in all market sectors: “If you don’t wish to have a future repeat of this crisis, in which. . .
- Your product liability increased, sometimes dramatically, because of the types and amounts of raw material substitutions that you were required to make
- Every day brought new crises and new challenges, albeit rarely challenges of the positive kind
- Everyone in the company felt a level of stress unthinkable in the past
- Valuable but burned-out employees left you dangling in the wind because they either retired early or sought employment in non-chemical industries
- You were forced to shed other highly knowledgeable employees so that you could keep your business afloat
. . .then you only have one way forward: everything must change.” Whether. . .
- Supply chain procedures and policies or product formulation practices
- Production procedures or logistics, both incoming and outgoing
- Policies governing both accounts payable and accounts receivable
- Stocking levels, both raw material and finished goods
. . .Everything needs to be re-examined in the light of the Supply Chain Crisis, and—with few exceptions—everything must be changed in ways previously not envisioned, but now necessary for the smoothest possible, and least vulnerable, operation heading into the future.
The supply chain crisis gave multiple industries the opportunities to learn from the past so that they could create safer, more secure, and more robust procedures in the future to guard against the failures that the entire globe had just experienced. Those that took advantage of this “tough love” type of learning have profited greatly and are more prepared than ever to tackle similar difficult times in the future, in a world where politics and historic enmities can tip everything on its side on a moment’s notice. Those that did not, sad to say, are just now beginning to feel the delayed impact of their lack of change to accommodate our new reality. Some are struggling to keep their heads above water. Others have either drowned or are in the process of drowning. It is sad, but predictable. The one weapon that every paint, coatings, adhesives, and sealants raw material supplier and product producer has at its disposal is the ability to create a strategy that takes into consideration the lessons learned during the Great Supply Chain Crisis, and apply this learning to the careful creation of a winning strategy for the future. The creation of, and adherence to, such a strategy will not only keep businesses from repeating the mistakes of the past, but also place them in the best possible position to deal with similar situations in the future. Such strategies not only prepare organizations to avoid serious damage, but also arm them to take advantage of opportunities that inevitably arise during any period of time in which chaos reigns, whether regionally or globally.
The greatest opportunities for securing the future against unexpected, and potentially globally destabilizing, shortages are centered on securing access to supplies of raw materials that will enable coatings producers and their raw material suppliers to keep the wolf from the door for at least as long as a “worst case scenario” developed through risk analysis protocol suggests would be necessary. Sounds simple enough. . . .but, of course, it has many elements that must be anticipated and put into place in advance of the occurrence of a critically disruptive event. No longer can supply chain managers afford to chase every raw material penny down to the bottom of the barrel—we all saw, in 2021-2022, what happened to formulators who had treated their raw material suppliers as lesser forms of life, whereas formulators who valued raw material suppliers and who treated them as partners faced far fewer difficulties in obtaining desperately needed materials than the “C List” customers. (And yes—there is a scale of customers kept by raw material suppliers that typically rank them from “A” to “C,” which is why it wasn’t that uncommon during the Supply Chain Crisis for a relatively small customer to be given delivery precedence over a very large, but less user-friendly, customer.)
At the same time, raw material suppliers need to be incentivized to develop new products that will generate sufficient sales and margins to justify their investment in R&D. We saw, during 2022-2023, both the positive and the negative results that arose as a result of properly treated and incentivized raw material suppliers vs. those that were not. Consequently, far fewer new raw materials were introduced into commerce during that period of time. Midway through 2024, however, it appears that the tide has turned, and raw material producers are once again able to begin supporting the development of strategically important materials for the paint and coatings industry that are intended to address such global strategic issues such as unpredictable PFAS regulatory action and the increasing interest in giving “sustainability” true support, rather than just lip service. (Although some aspect of “sustainability” fits within the target goals of ESG, it is only one aspect among many. While ESG is an important concept, and worthy of significant discussion, it is a concept far too broad to discuss within the context of this article, which truly is devoted to the concepts of both “sustainability” and “new raw materials.”)
Among the broad array of raw material suppliers, distributors, and coatings producers with whom the author is in regular contact, most do not foresee significant supply chain disruptions during 2024, but everyone adds one or more of the following conditional phrases, “We don’t see any significant supply issues, assuming that:
- We do not have a significant and unexpected economic event in, or directly affecting, the U.S.”
- The War in Ukraine, the War between Israel and Hamas, the Houthi rebel activity in the Red Sea or the Chinese cause anything to disrupt the global supply chains to a greater degree than has already been the case.”
- Interest rates do not begin to rise again.”
- PFAS discussions do not result in the regulatory version of an atomic bomb.”
There are quite a few qualifiers in play here, but this is probably as realistic as it is possible to be at this point in time. Many of these companies are giving precedence in their thinking to tactical, rather than strategic matters, and that is a natural thing to do, but it isn’t going to do much more than keep them afloat for the near-to-mid-term. Only by looking at the future through the lens of strategy can companies create plans to position themselves to take maximum advantage of opportunities and minimize threats from outside forces.
If the supply chain issues and high inflation of the past few years have taught the industrialized world one thing, it is that no manufacturing business can afford to keep all of its eggs in one basket—single-sourcing from raw material producers is dangerous; single-sourcing from individual countries is even more so; and failing to source at least some portion of as many raw materials as possible from the geographic region in which the customer is situated is simply asking for problems. Every player in the paint and coatings value chain that wants to have as bright a future as possible needs to assimilate, and act upon, a few timeless lessons that were highlighted on a global basis during the past three years:
- JIT (just in time delivery) is dead—or if not yet dead, at least in a state of dying. Unless you are a very large customer that is the final link in your supply chain, JIT is your enemy, not your friend.
- Every raw material used to make paint and coatings in the U.S. should have at least one reliable vendor in the U.S. that either makes the material in the U.S. or has significant stocking capability in the U.S.
- Having a single source of any raw material is a bad idea, even if it is sometimes necessary due to the absence of a second source.
- Certain high-profile manufacturing operations should be repatriated to the U.S., as should the ancillary suppliers to those industries.
- It is also good to have a low-profile but ongoing R&D effort to investigate potential raw material substitutions and have specifications, instructions for use, and product names readily available in the case of shortages.
- Finally, and most importantly, even during the darkest hours when all hands are on deck trying to put out fires, absolutely nothing should prevent an appropriate level of true R&D from taking place. Coatings is a technology-based, global industry, and at the end of the day those with a strategy focused on the continual development of new and improved products will be the winners.
The Current Supply Chain from the Perspective of Specialty Chemical Suppliers
China recovered uncharacteristically slowly from the economic damage that it incurred as a result of COVID, and it hasn’t been purchasing nearly the raw materials for in-country use that would have been the case if things hadn’t been so hampered by closures. China is now, however, beginning to draw on raw materials again for internal use, and we need to be ready for that. This is not yet a supply issue—China’s economy has by no means recovered from the combination of COVID and the supply chain crisis that followed, and it is facing substantial economic challenges, including deflation, an unstable housing market, significant declines in domestic stock markets, and a level of foreign investment in 2023 that was the lowest in the past three decades.[1] Nonetheless, there is likely to be a recovery in the future, and this is exactly the sort of situation that a properly prepared strategy contemplates and creates options for dealing with such eventualities if/when they occur.
No one can plan for every conceivable eventuality in a complicated world, but a carefully planned strategy enables a management team to plan for disruptive events that are at least likely to occur in the coming 5-10 years, whether such events involve major weather events such as the “Big Freeze” in the Permian Basin/Texas in February 2021, crude oil manipulation by OPEC or other major oil-producing nations, wars, recession, or economic recovery by China.
Beyond raw material availability at the producer, another major cause of shortages and steep price increases between January 2020 and January 2023 was the cost of transoceanic shipping containers, which rose dramatically from approximately $1,500-$2,500 for non-hazardous loads in late 2019 to as much as $20-$21K (even as high as $30K in specific incidences) by mid-2021, before dropping back to the deceptive “new low” of roughly $1,300 in January of this year. Unfortunately, this is when the Iranian-backed Houthis initiated what is now called the “Red Sea Shipping Crisis.” Thirty percent of global container trade passes through the Suez Canal, and shipping costs have risen as much as five-fold on routes from Asia to Europe. From January-April 2024, the cost to ship a 40-foot container from China to the U.S. went from $1,300 to as high as $4,400 in March, before declining to $3,300 in April. What happens to the cost of container shipping in the months ahead is anybody’s guess, but it is difficult to see it settling back to $1,300 anytime soon, even if the Red Sea Shipping Attacks were to stop tomorrow (Figure 1). J.P. Morgan estimates that the disruptions could add 0.7 percentage points to global core goods inflation, and 0.3 percentage points to overall core inflation, during H1 2024.[2]
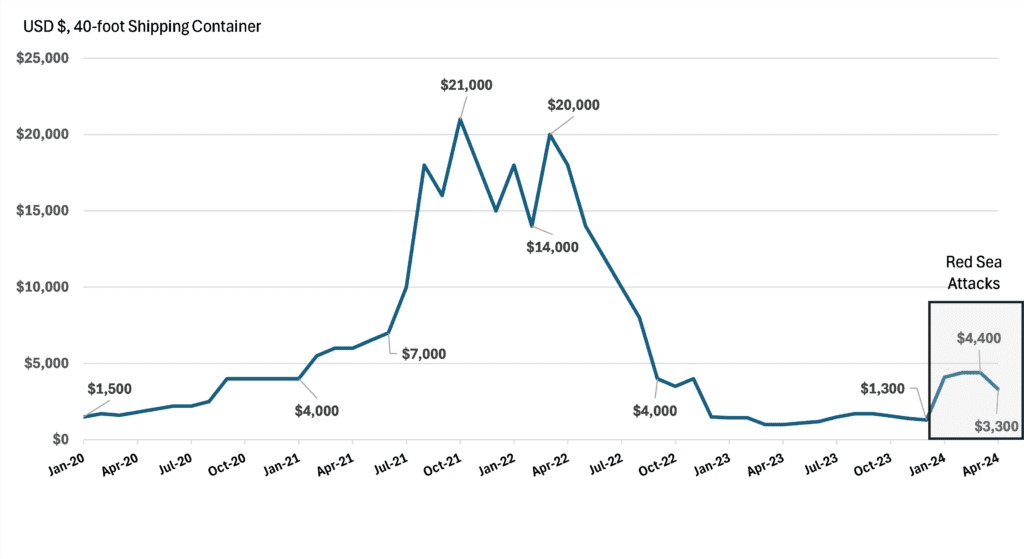
(Source: Freightos FBX, The ChemQuest Group, Inc.)
Meanwhile, U.S. long-distance trucking rates declined between January 2022 and January 2023, but the decline hasn’t been to nearly the level that prevailed in January 2019 (Figure 2) and U.S. rail transportation of freight steadily rose between January 2020 and January 2024 (Figure 3).
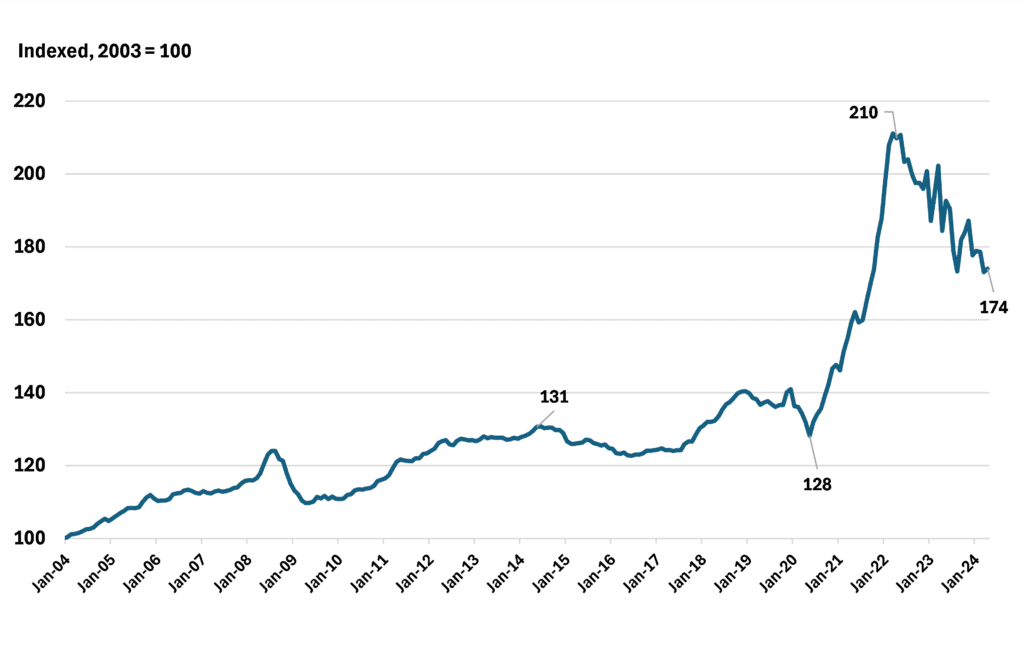
(Source: Federal Reserve Bank of St. Louis, The ChemQuest Group, Inc.)
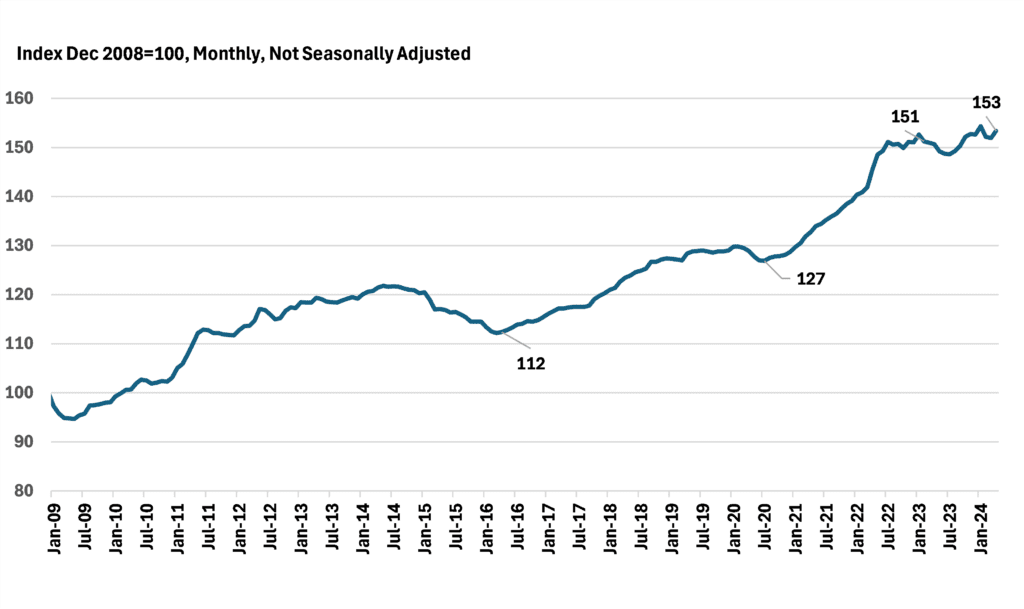
(Source: Federal Reserve Bank of St. Louis, The ChemQuest Group, Inc.)
Is the U.S. Economy in the Process of “Resetting”?
There is little doubt that not just the U.S. but the entire global community is being “reset” to one degree or another—and in one aspect or another. While we may be too close to the overall situation to see all of the subtleties, it is reasonable to envision a continuum from 2021 through 2025 in high-level terms that nonetheless should have some degree of meaning for everyone in the U.S. paint and coatings industry with regard to overall market dynamics during this period of time:
1. 2021—”The Supply Chain Train Wreck” was initiated by the February 2021 Great Freeze in the Permian Basin and exacerbated by the subsequent supercell storms, hurricane-force winds, baseball-sized hail, severe flooding, and large numbers of tornadoes in the region throughout the remainder of the year. This was further complicated by an explosion at a major alkyd resin supplier; a fire at a second major resin producer; and the withdrawal from the market of a number of resins by a third major producer.[3]
2. 2022—We experienced some degree of recovery in Q3-Q4 with regard to lead times and availability, but a significant period of inflation set in as demand increased, unemployment hit historic lows, and cost of labor soared for the industry as a whole. The typical R/M cost increase for a basket of coatings raw materials between Q1 2020 and Q4 2022 was roughly 40-50% (Figure 4).
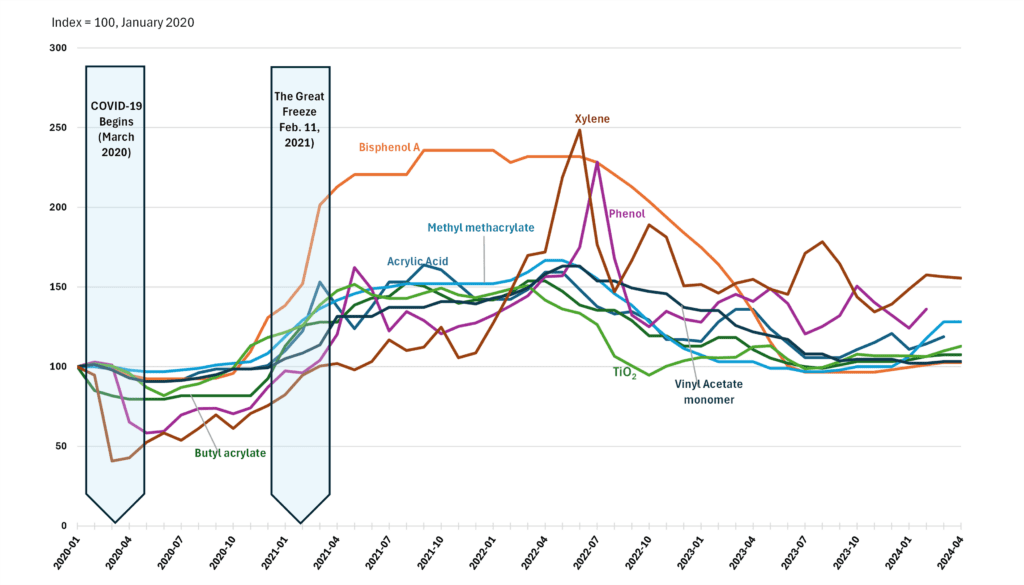
(Source: ChemQuest estimates, Coatings TraQr®)
3. 2023—This was a year of the market trying to right itself, but with less-than-stellar success—supplies and prices began to normalize gradually throughout the year, but the cost for the same basket of raw materials from Q4 2022 was only down by approximately 30%by Q4 2023.
4. 2024—Barring a major intervening global/economic event, most raw materials should be readily available, but pricing is unlikely to sustain any additional reductions.
5. Sales of both new and existing homes is improving slightly during H1 2024, but there is simply no question that the country is in a deep hole with regard to housing—per the National Association of Home Builders (NAHB),[4] there is a nationwide shortage of roughly 1.5 million housing units. This clearly reflects the mixed emotions of both the public and the construction industry on a number of fronts, including the overall health of the economy; the risk of further inflation; the significant increase in the price of housing; the stability of the financial markets; and the labor supply. Also, as a result of the move from work offices to home offices, there is an oversupply of offices and office buildings that is unlikely to be brought into balance before 2029-2030.
6. 2025—The “New Normal” will have been reached by Q4, with regard to the availability of raw materials and stabilized pricing. Mortgage rates will decline, leading to improved activity in the sale of existing, and construction of new, homes. Supply and demand in residential units is unlikely to be in balance until 2029.
What is Going to Become of the R&D Efforts in the Coatings Industry?
Quite understandably, there wasn’t an abundance of new products offered by the paint and coatings producers or their raw material suppliers between 2019 and 2023 due to the need for “all hands on deck” to deal with both raw material substitutions and to assist with finding and approving new sources of raw materials. There is no need to be concerned that there aren’t any new raw materials around, however—the increasing move of the specialty chemical industries to embrace ESG (“Environmental, Social and Governance”) as a part of strategic planning; the increasing interest of both businesses and the public in the environment; the fact that sustainability is the subject of growing, and very serious, interest around the globe; and the initial regulatory fiat emerging in the PFAS arena will guarantee a steady flow of new raw materials for all businesses that either make or use specialty chemicals. A random look around in H1 2024 brought to my attention many new raw material introductions that met the criteria that I have used in past years for inclusion in my articles. Materials:
- That have been introduced into general commerce with the past 18-24 months
- That their producers affirm are not just “tweaks” on existing products
- That definitely hold the potential to create properties in certain paint and coatings systems that do not currently exist, or significantly improve properties in materials that do.
I see many such materials every year, and—without endorsing or recommending any of them, either on behalf of myself, the ChemQuest Group, or PCI Magazine—I am including some of them in Table 1 because these products, while chosen both randomly and arbitrarily, are likely to make sense for paint, coatings, adhesive, and sealant formulators (and perhaps other specialty chemical producers, as well) to evaluate, especially if the descriptions of the new materials (provided by their manufacturers) in the tables appear to address any properties that would be helpful in creating new commercial formulated products.[5]
Table 1. Examples of New Raw Material Introductions
Supplier | Product Name | Raw Material Type | Manufacturer’s Suggested Use(s) | Email, Telephone, or “Contact Us” Form | URL |
Allnex GmbH | CRYLCOAT® E 04930 | Solid Resin | TGIC hardened binder with excellent ink and label adhesion as well as superior outdoor resistance developed for general industrial metal applications. The product’s unique surface energy properties allow for ease of print or label adhesion. | allnex.com/en/Contact-Us | allnex.com/en |
Allnex GmbH | SETACQUA® 6302 | Resin | Improved pigment grinding resin that further imparts stain- and chemical-resistant properties to base formulations in industrial coatings and decorative wood applications. | allnex.com/en/Contact-Us | allnex.com/en |
Allnex GmbH | Setal® 21-3610 | Liquid Alkyd, High Bio-renewable Content | Long oil alkyd for traditional SB deck stain applications; 97% solids, with 70% BETA Analytic certified bio-based content. Deep penetrating performance, weatherability and long-term wear expected of oil-based alkyds for exterior wood | allnex.com/en/Contact-Us | allnex.com/en |
Allnex GmbH | Ebecryl® 115 | Trifunctional Energy Curing Diluent | Inks and coatings where TMPTA-free solutions are required. TMPTA’s recent reclassification has left many formulators searching for a safer alternative. Ebecryl® 115 delivers all of the expected properties and requires minimal reformulation of inks and coatings. | allnex.com/en/Contact-Us | allnex.com/en |
Allnex GmbH | ADDITOL XL 6592 | 100% Active Universal Dispersant | Universal usage in solvent-based, water-based, UV-cured, and powder systems; high pigment loading across most pigments systems, including fillers and extenders; enhances corrosion, water, humidity, and weather resistance. | allnex.com/en/Contact-Us. | allnex.com/en |
BYK USA Inc. | BYK-1810 BYK-BYK-1811 BYK-1815 BYK-1816 BYK-1818 | Defoamers | PFAS-free, silicone-containing defoamers for solventborne and solvent-free systems; high efficiency and excellent spontaneous defoaming on a par with PFAS-containing products. | Additive Guide – BYK: byk.com/en/product/additive-guide Ask.BYK.USA@altana.com (USA only) 203-678-7328 (USA) Contact—BYK (Global) | Byk.com |
BYK USA Inc. | CERAFLOUR 1003 CERAFLOUR 1004 | Wax Additives | 100% bio-renewable, corn starch-based wax-like polymers; good matting efficiency while keeping optimum transparency; CERAFLOUR 1003 imparts slight surface structure and provides a similar matting effect at different observation angles: CERAFLOUR 1004 has finer particles for a slight matting effect combined with high transparency and a smooth, soft and silky feel. | Additive Guide – BYK: byk.com/en/product/additive-guide Ask.BYK.USA@altana.com (USA only) 203-678-7328 (USA) Contact—BYK (Global) | Byk.com |
BYK USA Inc. | CERAFLOUR 1010 | Wax Additive | Sustainable, 100% bio-renewable, rape seed-based wax additive for high matting and mechanical resistance; excellent matting effect; high mechanical resistance; suited for modern wood coatings systems, like natural look formulations. | Additive Guide – BYK: byk.com/en/product/additive-guide Ask.BYK.USA@altana.com (USA only) 203-678-7328 (USA) Contact—BYK (Global) | Byk.com |
BYK USA Inc. | BYK-1880 | Defoamer | Solventborne and solvent-free systems applied by airless or air-assisted airless spray; silicone-containing; specifically recommended for two-pack high-solids PUR systems but can also be used in conventional spray-applied systems. | Additive Guide – BYK: byk.com/en/product/additive-guide Ask.BYK.USA@altana.com (USA only) 203-678-7328 (USA) Contact—BYK (Global) | Byk.com |
BYK USA Inc. | BYK-3558 | Surface flow and leveling additive | Improves leveling and prevents cratering in high- and medium-solids coating systems; combines the beneficial properties of silicones and polyacrylates in a well-balanced manner in one product for perfect surfaces in solvent-reduced high- and medium-solid coating systems. | Additive Guide – BYK: byk.com/en/product/additive-guide Ask.BYK.USA@altana.com (USA only) 203-678-7328 (USA) Contact—BYK (Global) | Byk.com |
Cabot Corporation | MAJESTIC® 710 | Highly dispersible Carbon Black | Easy-to-use pigment for waterborne system. It enables a more sustainable and cost-effective color solution by reducing the processing time and dispersant loading significantly. | performance.na@cabotcorp.com | Cabotcorp.com |
Cabot Corporation | ATHLOS™SR1200 | Carbon Nanostructures (CNS) | Delivers an exceptional combination of conductivity and light color. This new and unique nanomaterial enables formulators to achieve a lighter, smaller, thinner, and more conductive coatings solution without sacrificing strength. | Performance.na@cabotcorp.com | Cabotcorp.com |
Cardolite | LITE 513DF | Epoxy Diluent/Modifier | CNSL-based, high bio-content, multi-functional epoxy diluent and modifier suitable for use in coatings, one- and two- component adhesives and composites; excellent corrosion and cathodic disbondment protection while increasing flexibility and lowering viscosity. | Contact: marketing@cardolite.com | cardolite.com |
Cardolite | NX-5660 | Epoxy Curing Agent | CNSL-based, solvent-free, low viscosity phenalkamine for use in ultra-high solids and solvent-free marine and protective epoxy coatings; widens application window by offering very fast cure in all seasons; good intercoat adhesion even under harsh cure conditions. | marketing@cardolite.com | cardolite.com |
Chan Sieh Enterprises Co., Ltd. | Polyurethane Dispersion L-2903M | PUD | Air-dry topcoats and clears; excellent adhesion to metals and plastics; good alcohol miscibility; can be used for waterborne aerosol coatings. | Call: Jim Kuo, +886-2-25816516, Ext. 1122 | chansieh.com.tw |
Chan Sieh Enterprises Co., Ltd. | Polyurethane Acrylic L-3950 | PUDA | High-temperature bake; extremely high hardness; excellent chemical resistance. | Call: Jim Kuo, +886-2-25816516, Ext. 1122 | chansieh.com.tw |
EPS | EPS® 2786 | All-acrylic, MFFT 21 ˚C | Interior/exterior; near-zero VOC without fluorosurfactants; hot block resistance. | Contact Karl Booth: kbooth@eps-materials.com Office: 815-568-4829; Mobile: 815-208-2551 | epscca.com |
EPS | EPS® 2585 | Styrenated Acrylic | <100 g/L VOC-capable DTM coatings; hardness, flexibility, corrosion resistance; exterior durability. | Contact Karl Booth: kbooth@eps-materials.com Office: 815-568-4829; Mobile: 815-208-2551 | epscca.com |
EPS | EPS® 2210 | All-acrylic | Topcoats capable of conforming to ASTM D6083 Type II standards. | Contact Karl Booth: kbooth@eps-materials.com Office: 815-568-4829; Mobile: 815-208-2551 | epscca.com |
EPS Engineered Polymer Solutions | PC-Mull 815 | Bio-based acrylic copolymer | High-performance furniture and wood finishes; exceptional transparency, hardness, leveling, chemical, and block resistance; commercial in EMEIA markets | North America: www.coatingsadditives.com Phone: 1-800-654-4242 | epscca.com |
Evonik Industries AG | SPHERILEX® EXP 0002-1 | Matting, Haptics | Spherical silica, small particle size, and suitable for architectural paints, as well as waterborne, deep-matte and silk-gloss wood coatings. | corporate.evonik.com/en/products-and-solutions/search-our-products | corporate.evonik.com/en |
Evonik Industries AG | TEGO® Flow 380 | Additive | Suitable for solventborne coatings, especially clear coats. Low viscosity; very low VOC. | corporate.evonik.com/en/products-and-solutions/search-our-products | corporate.evonik.com/en |
Evonik Industries AG | VISIOMER® HEMA-P 100 | Monomer | Phosphate methacrylate monomer, provides transparent flame retardancy, improves adhesion and corrosion resistance. | corporate.evonik.com/en/products-and-solutions/search-our-products | corporate.evonik.com/en |
Evonik Industries AG | TEGO Foamex 11 | Siloxane-based defoamer emulsion | Optimized for high-PVC coatings; 15% active ingredient; more environmentally friendly than traditional mineral oil-based defoamers | https://www.coating-additives.com/en/evonik-presents-new-tego-foamex-defoamers-performing-sustainability-in-architectural-coatings-243437.html | coatingsadditives.com |
Evonik Industries AG | TEGO Foamex 16 | Siloxane-based defoamer concentrate | Provides exceptional balance of defoaming efficiency and compatibility; especially effective in low-to-medium PVC coatings; contains 25% bio-based material | https://www.coating-additives.com/en/evonik-presents-new-tego-foamex-defoamers-performing-sustainability-in-architectural-coatings-243437.html | coatingsadditives.com |
FP® Pigments | FP-440 | FP-Opacity Pigment™ | Optimally spaced TiO2 for scattering; high refractive index of | Contact Paul F. Dietz: paul.dietz@fp-pigments.com Office: +44 (0) 1429 282 369; Mobile: +44 (0) 788 145 4949 | fp-pigments.com |
Integrity Biochem | TegraP&C ICS 31– RCI 94% and TegraP&C ICS 32-RCI 61% | Biobased “Tunable Range” of surfactants | Biobased, domestically sourced; zero VOC; RCI (“Renewable Carbon Index) between 61-94%: APEO-free | E-mail: dkotowski@umccorp.com Phone: Dave Kotowski at 216-577-1982 | integritybiochem.com www.umccorp.com |
Lubrizol | Turboset™ 5000HS | PUD | High solids, self-crosslinking PUD; high-traffic wood floor coatings; 50% weight solids. | Contact Nick Sterne: Nicholas.sterne@lubrizol.com Office: 216-447-5799; Mobile: 301-465-9018 | Lubrizol.com |
Lubrizol | PowderAdd™ 9780 | Texturing Agent | PTFE-free texturing agent; uniform texturing effect in powder coatings without the use of PTFE or other PFAS. | Contact Nick Sterne: Nicholas.sterne@lubrizol.com Office: 216-447-5799; Mobile: 301-465-9018 | Lubrizol.com |
Lubrizol | Solsperse™ 29000 | Pigment Dispersant | 100% active flowable dispersant with >50% bio-based content for S/B and UV-cured coatings; improved pigment dispersion and stability in low-to-medium polarity liquid organic media. | Contact Nick Sterne: Nicholas.sterne@lubrizol.com Office: 216-447-5799; Mobile: 301-465-9018 | Lubrizol.com |
Lubrizol | Solsperse™ 77500 | Pigment Dispersant | High-performance for S/B systems; 40% active polymeric dispersant; helps achieve low viscosity and high pigment loadings; rapid color strength development. | Contact Nick Sterne: Nicholas.sterne@lubrizol.com Office: 216-447-5799; Mobile: 301-465-9018 | Lubrizol.com |
Lubrizol | Solsperse™ W150 | Pigment Dispersant | 100% active, flowable, for aqueous coatings; active across broad range of pigments and fillers. | Contact Nick Sterne: Nicholas.sterne@lubrizol.com Office: 216-447-5799; Mobile: 301-465-9018 | Lubrizol.com |
Micro Powders, Inc. | Superslip 6515AL-EZ | Surface Lubricity and Wear-resistance Additive | Easy-to-disperse PFAS replacement; surface-treated version of Superslip 6515AL; maximum scratch resistance equal to PE/PTFE additives; good abrasion resistance and excellent antiblocking and release properties. | info@micropowders.com (914) 793-4058 | micropowders.com |
Micro Powders, Inc. | MicroMatte 1415 | Multifunctional Matting Additive | Improves soil release and dirt pickup resistance in architectural coatings; complex wax composite dramatically improves DPUR vs. inorganic flattening agents; provides efficient gloss reduction; not classified as a microplastic. | info@micropowders.com (914) 793-4058 | micropowders.com |
Micro Powders, Inc. | MicroTex 580 | PFAS-free biopolymer additive for powder coatings texturing | Imparts a uniform sandpaper-like surface texture when formulated in a matte polyester/acrylic system; in polyester/epoxy and polyester/HAA systems, provides a smoother, scattered granular surface texture. | info@micropowders.com (914) 793-4058 | micropowders.com |
Micro Powders, Inc. | Microspersion 510E | Nonionic polyethylene wax emulsion surface Lubricity and wear-resistance additive | Imparts slip, scuff, and abrasion resistance; improves mar resistance, block resistance and slide angle of water-based inks, coatings, and overprint varnishes; adds early water resistance; broad global food contact compliance. | info@micropowders.com (914) 793-4058 | micropowders.com |
OQ Chemicals | OxBalance Isononanoic Acid | Monomer | Isononanoic acid produced from both bio-based and circular feedstocks, certified by the International Sustainability & Carbon Certification (ISCC Plus) agency. | Sc.communications@oq.com | Chemicals.oq.com/company |
The Shepherd Color Company | Starlight FL170 | Special Effect Pigment | Glass flake with pure metallic silver coating for bright, intense sparkle; easily dispersed in liquid coatings; stable in waterborne systems; robust enough for extrusion into powder coatings. | mryan@shepherdcolor.com | Shepherdcolor.com |
The Shepherd Color Company | Arctic IR Black 10F925 | CI Brown 29 | Deep black with IR properties to allow sorting of black materials in plastics recycling; improves sustainability of plastic materials through increased recyclability; food contact substance under FDA FCN#002206. | mryan@shepherdcolor.com | Shepherdcolor.com |
Shin-Etsu MicroSi-Nissan Chemical | CHALINE R-175S | Non-film-forming powder silicone-acrylic polymer additive | Additive for plastics or synthetic leathers in extrusion/injection molding, calendar molding, or casting molding; synthetic rubber applications; surface properties such as slip functionality, abrasion resistance; surface texture/feel improvement; soluble in solvents. | Team: Coatings@microsi.com 480-893-8898 Ian Holden: iholden@microsi.com Cathy Parker: cparker@microsi.com | www.microsi.com Nissin Chemical Industry Co., Ltd. (nissin-chem.co.jp) |
Shin-Etsu MicroSi-Nissan Chemical | CHALINE R-200 | Non-film-forming powder silicone-acrylic polymer additive | Additive for plastics or synthetic leathers in extrusion/injection molding, calendar molding, or casting molding; synthetic rubber applications; surface properties such as slip functionality; abrasion resistance; surface texture/feel improvement; not soluble in solvents. | Team: Coatings@microsi.com 480-893-8898 Ian Holden: iholden@microsi.com Cathy Parker: cparker@microsi.com | www.microsi.com Nissin Chemical Industry Co., Ltd. (nissin-chem.co.jp) |
Syensqo | Rhodoline HBR | Non-PFAS coating additive | Non-fluorosurfactant alternative for established fluorine-containing additives | https://www.syensqo.com/en/innovation/pfas | syensqo.com |
Viridis™ Chemical Company | Renewable Ethyl Acetate—Urethane Grade | Solvent | 100% low-carbon, bio-based ethyl acetate helps customers to meet Scope 3 GHG reduction goals when compared to typical petroleum-based production technologies. | Steve.friedewald@worldsearchconsultancy.com 214-552-8171 | worldsearchconsultancy.com |
Wuhan Yincai Technology Co., Ltd. | L2018C | Matting Agent for Outdoor Powder Coatings | Low wax content, addition-type outdoor matting agent; used at 3-6% of total formulation in PE/TGIC system results in 5-50% reflectance @60˚. | weixu@yin-cai.com; Call: Wei Xu, +1 715-699-9160 | yin-cai.com |
Zschwimmer & Schwarz Chemie GmbH | SYNTRAN AC 5199 | hydroxy functional styrenated acrylic emulsion | Low-temperature cure with melamine or isocyanate curatives; does not require any additional catalysts to fully cure with an appropriate crosslinker. The resulting coating demonstrates excellent physical properties on various substrates, and improved adhesion and load capacity compared to similar technologies. | Ryan Yaworski, r.yaworski@zschimmer-schwarz.com 330.283.3415 or Tony Turoso, t.turoso@zschimmer-schwarz.com 502.930.6360 | Zschwimmer-Schwarz.com.en |
Zschwimmer & Schwarz Chemie GmbH | SYNPRINT AC 5918 | Surfactant-free, multiphase, self-crosslinking acrylic polymer | Very fine particle size; clear in the can; polymer film exhibits excellent transparency even at high film thicknesses (400-500 µm wet film); suitable for outdoor and indoor coatings as well as water-resistant inks; low foaming and extremely low water absorption; can be blended with hard acrylics to reduce the MFFT, and with PUDs for exterior applications. | Ryan Yaworski, r.yaworski@zschimmer-schwarz.com 330.283.3415 or Tony Turoso, t.turoso@zschimmer-schwarz.com 502.930.6360 | Zschwimmer-Schwarz.com.en |
Zschwimmer & Schwarz Chemie GmbH | SYNTRAN AC 2901 & 2902 | Inherently matte acrylic polymers | Low gloss, high flexibility, and good stability while providing excellent adhesion to various substrate types without the additional use of waxes or powdered matting agents; gives a slightly soft touch to the surface; can be used to produce matte formulations without affecting the color of the ink or the substrate; AC 2901 yields a softer touch coating feel, while AC 2902 offers a slightly harder film. | Ryan Yaworski, r.yaworski@zschimmer-schwarz.com 330.283.3415 or Tony Turoso, t.turoso@zschimmer-schwarz.com 502.930.6360 | Zschwimmer-Schwarz.com.en |
Zschwimmer & Schwarz Chemie GmbH | SYNTRAN AC 1012 | Non-film forming W/B acrylic polymer | Use as an additive (5-20%) in formulations to improve hardness, sandability and block resistance; 100% styrene free and will form a continuous film with the appropriate coalescent solvent level or drying temperature; compliant with FDA CFR 175.105 and CFR 176.180; suitable for use in coatings and graphic arts applications for indirect food contact. | Ryan Yaworski, r.yaworski@zschimmer-schwarz.com 330.283.3415 or Tony Turoso, t.turoso@zschimmer-schwarz.com 502.930.6360 | Zschwimmer-Schwarz.com.en |
What Lies Ahead?
The coatings industry is still reeling from three very stressful years in which more than just the supply chain, raw material shortages, late deliveries, and skyrocketing prices were problems. The loss of key personnel, along with their collective experience, who either burned out and left the industry or who simply couldn’t stand the stress and retired much earlier than they had planned, will be felt by the paint and coatings industry for years to come, especially in the technology and marketing areas. Such experience is developed slowly and deliberately over significant periods of time and cannot be recreated or duplicated in the short term. Once it is gone, it is gone, and this should be the most sobering and thought-provoking takeaway from this article.
As a result, raw material suppliers and paint producers are looking to universities, independent third-party technology institutions like ChemQuest, third-party testing laboratories, and independent subject matter experts to supply them with the experience that was once “in house” but has now disappeared and cannot be backfilled with other personnel who lack sufficient experience and expertise. At ChemQuest, we are actively helping manufacturers in the specialty chemicals value chain deal with the effects of this loss of experience, whether in paints and coatings; adhesives and sealants; lubricants; personal care; HI&I; and a variety of other areas. Although both a period of global crisis and long-term poor management by many producers caused the situations that precipitated this loss of valuable expertise, a timely opportunity has arisen to explore the experience and creativity of highly experienced, independent paint and coatings experts who bring a wealth of technical and marketing knowledge and operational know-how to bear upon the challenges and opportunities of the paint and coatings producers who seek their help to solve a universe of diverse issues in an efficient, cost-effective manner.
This is very likely to be the wave of the future, in which cross-functional in-house resources, working with independent experts, will be the most efficient and cost-effective approach to meeting increasingly demanding time-to-market requirements with appropriate new products.
To learn more, reach out to the author at gpilcher@chemquest.com.
Read in PCI.
References
1. “Overview: The World Bank in China,” updated April 2024, https://www.worldbank.org/en/country/china/overview#:~:text=Domestic%20demand%20in%20China%20has,to%20undergo%20a%20structural%20slowdown.
2. “What are the impacts of the Red Sea shipping crisis?” J.P. Morgan, February 2024, https://www.jpmorgan.com/insights/global-research/supply-chain/red-sea-shipping#:~:text=Overall%2C%20J.P.%20Morgan%20Research%20estimates,transport%20times%20and%20freight%20costs.
3. Pilcher, G.R., “The Great Supply Chain Fiasco of 2021-2022: The Immediate Danger is Past, but What Lies Ahead?” CoatingsTech, 2023, 20 (3), pp. 30-40.
4. Thompson, E., “Single-Family Starts will Rise in 2024 but Supply-Side Challenges Persist,” National Association of Home Builders, February 2024, https://www.nahb.org/news-and-economics/press-releases/2024/02/single-family-starts-will-rise-in-2024.
5. Pilcher, G.R., “The Great Supply Chain Fiasco of 2021-2022: The Immediate Danger is Past, but What Lies Ahead?” loc. cit.