Table of Contents
Different aesthetic requirements for powder coatings necessitate formulators to be able to produce finishes in any level of sheen, from full gloss down to dead matte. By default, a basic powder coating formulation will exhibit a 60° specular gloss of 90 or higher. A number of different methods can be employed to reduce the luster to a semi-gloss or matte finish. Some of these techniques involve the incorporation of mineral fillers or wax additives to impart the desired appearance, while others utilize resin chemistry to create a microscopic texture on the coating’s surface.
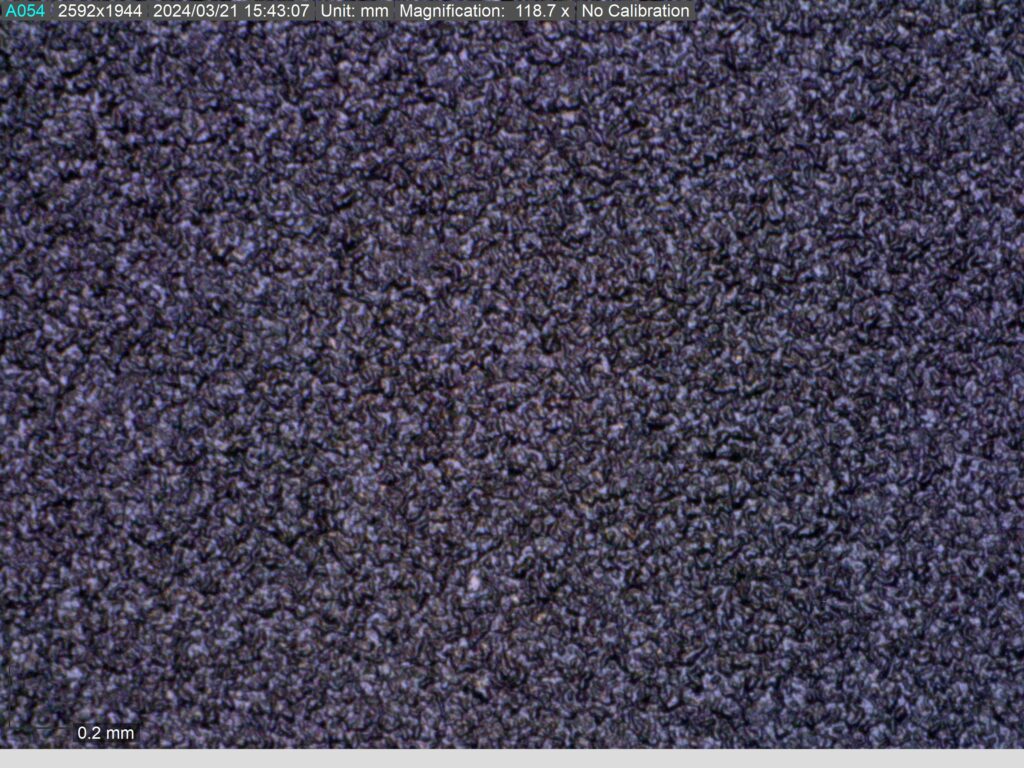
Extender Pigments
Extender pigments are inert, typically inorganic filler materials that are added to the formula to reduce overall formula cost but can also provide an aesthetic or performance-enhancing function. The most commonly used extenders in powder formulating are calcium carbonate and barium sulfate, though the particle size distribution of the mineral filler has more influence on the appearance of a powder coating than the chemical makeup.
Powder coatings are sensitive to high oil-absorption components such as fumed silica and organoclays. Whereas solventborne liquid coatings can incorporate high levels of fine particle size fillers for their matting needs, the viscosity of powder coatings increases incrementally with the incorporation of high oil-absorption additives to the point of extreme texture and film incontinuity. If used at a low level (e.g., under 4% by formula weight), they can decrease gloss or impart a subtle texture without losing mechanical properties.
On the other end of the particle size spectrum, larger particle size extender pigments may be used to affect a powder coating’s sheen. Particles larger than 44 microns (325 mesh) may protrude from the surface, creating unattractive defects known as bits or seeds. However, mineral fillers with a narrow particle size distribution and a median in the 10-20 micron range can disrupt the surface in a uniform way, creating a semi-gloss finish of 50 gloss units or lower.
This method is particularly viable in dark coatings that only require a low loading level of colorant pigment to attain opacity. In white or pastel coatings that require a higher loading of prime pigments, it may be difficult to incorporate enough filler to substantially reduce the gloss.
Wax Additives
Waxes used in powder coatings are typically synthetically produced and are characterized by their melt point. They are nominally incorporated at a level of 0.5-5.0%. Since powder coatings are normally extruded around 100°C, low-melting waxes like paraffin and carnauba melt below the typical extrusion temperatures and are intimately mixed with the polymeric binder during extrusion. Other waxes like Fischer-Tropsch and polyethylene are dispersed as a particle in the extruder and melt during the curing cycle, which can be up to 200°C or higher.
Either way, while the binder melts and cures in the oven, wax additives are driven to the surface of the coating; this positioning on the surface can have both positive and negative effects on the coating. On the positive side, the use of wax additives can improve the slip and mar properties of the coating. In addition, with proper selection, they can be used to reduce the gloss to as low as 40 gloss units.
However, if incorporated at too high of a level, they can impart haze and burnish, inviting fingerprints. They also can prevent intercoat adhesion in a multiple coat or recoat situation. Additionally, some waxes are not weatherable and not recommended for coatings requiring high UV durability. Because of these potential side effects, the formulator must take care to select the proper wax for gloss reduction and monitor coating properties at various addition levels to endure coating performance is not negatively impacted.
Type | Melt Point (°C) |
Paraffin | 50-70 |
Carnauba | 80-90 |
Fischer-Tropsch | 90-110 |
Polyethylene | 110-120 |
Polypropylene | 140-170 |
Polyamide | 260-270 |
PTFE* | >316 |
*PTFE is not a wax, but it is utilized in a similar way.
Differential Cure
Differential cure can be achieved by combining two compatible powder coating formulations with disparate functionality. The two components react and cure at different rates such that during the cure cycle, the faster-reacting components will crosslink, and flow will become restricted in those domains, while the slower-reacting components continue to flow. Finally, the slower-reacting components will crosslink. This differential-cure mechanism results in a microtexture on the film’s surface, which appears as a smooth, low-gloss finish.
One such tactic is the dry blend method, wherein two powder coatings, one with lower functionality (20-30 acid value) and one with higher functionality (50-70 acid value), are manufactured separately and blended in powder form. If extruded together, these resin systems typically do not result in a low gloss. When dry blended after they are manufactured, however, they can achieve a 60° gloss in the 20-40 range. This method is prevalent in Europe, using carboxyl acid functional polyesters cured with hydroxyalkylamide (HAA), which offers exterior durability.
One potential downside to the dry blend approach is that there is a characteristic “sparkle” appearance that can be seen on the surface of the coating and may not be desired, depending on the end-use application. There is also a possibility that the ratio of the two components could shift over time in an application system that reclaims powder and reintroduces it into the feed system.
One-shot matte formulating schemes (OSMs) are achieved by making a single formulation that contains two or more components that react at different rates during the curing cycle. This sometimes takes the form of a curing agent that comes pre-blended. One such product contains pyromellitic acid and an imidazole, both of which react with the epoxide groups in Bis-A epoxy resins, and is commonly used for gloss reduction in epoxy or polyester/epoxy hybrid coatings.
Alternatively, one-shot matte powder coatings can be formulated by including two resins with disparate levels of reactivity, each matched stoichiometrically with the same curing agent. This method is particularly effective with polyester/urethane systems, where hydroxyl-functional polyester resins vary widely in hydroxyl number from 20 to 300. These coatings can achieve a dead matte finish of less than 10 gloss units and can be used in exterior applications but require a high concentration of expensive blocked isocyanates, which can result in high formula cost.
The equivalent weight of a hydroxyl functional polyester is determined using a titration method in a two-step process. The resin is first dissolved in a solvent blend and then reacted with a multifunctional acidic compound. This resin is then titrated with potassium hydroxide (KOH). The hydroxyl number is a measure of milligrams of KOH, and the equivalent weight is calculated as such:
(Molecular weight of KOH x 1000) / Hydroxyl Value = Equivalent weight in grams
For this example, we will use a polyester with a hydroxyl value of 30, and one with an OH of 290:
Low OH polyester: 56,100/30 = 1870 grams per equivalent
High OH polyester: 56,100/290 = 193.4 grams per equivalent
The equivalent weight of a blocked isocyanate crosslinker can be calculated by dividing the molecular weight of the isocyanate group (NCO), which is 42 grams, by the percentage of isocyanate provided by the manufacturer.
15.2% NCO crosslinker: 42/15.2 = 275 grams per equivalent
To maximize the differential curing effect, the two fractions can be formulated each as 50% of the binder.
Low OH polyester: 1870 / (1870 + 275) = 0.87
0.87 x 50 = 43.59 parts per 100 total
Blocked isocyanate: 275 / (1870 + 275) = 0.13
0.13 x 50 = 6.41 parts per 100 total
High OH polyester: 193.4 / (193.4 + 275) = 0.41
0.41 x 50 = 20.64 parts per 100 total
Blocked isocyanate: 275 / (193.4 + 275) = 0.59
0.59 x 50 = 29.36 parts per 100 total
The same blocked isocyanate is used for each fraction, so combined together the binder portion of the formula would be as follows:
Low OH polyester | 43.59 |
High OH polyester | 20.64 |
Blocked isocyanate | 35.77 |
Total | 100.00 |
The ratio of the low OH and high OH portions can be adjusted to achieve a gloss higher than a dead matte (see Table 2). Increasing the share of the low OH fraction has the effect of increasing the overall flexibility of the coating and reducing the formula cost. Increasing the high OH part will in turn increase the level of isocyanate, resulting in increased chemical and scratch resistance due to the high level of crosslink density.
A | B | |
Low OH polyester – 20 to 50 30 OH EW = 1870 | 87% | – |
High OH polyester – 220 to 290 290 OH EW = 193.4 | – | 41% |
Blocked isocyanate 15.2% NCO EW = 275 | 13% | 59% |
In recent years, resin manufacturers have begun to offer carboxyl-functional polyester resins for one-shot matte formulations. Cured by either TGIC or HAA, these polyesters can feature excellent UV durability at a reasonable cost.
Incompatible Resins
Another method of achieving low gloss in a single formulated product is to combine two incompatible polymers in a one-shot formulation. Carboxyl functional polyesters can react readily with the epoxide groups on glycidal methacrylate (GMA) functional acrylics.
Specialized GMA acrylics used in these formulations are designed to have a certain amount of incompatibility with the polyesters (often referred to as “controlled incompatibility”). When these coatings cure, a microscopic structure of hills and valleys is produced on the surface and can result in an attractive dead matte finish of 5 gloss units or less.
Formulators can replace some of the GMA acrylic with a curing agent such as TGIC or HAA to finely tune the gloss level to any target value between matte and full gloss. These coatings can have excellent outdoor durability, as well as chemical and scratch resistance.
The equivalent weight of acid-functional polyesters is calculated similarly to the previous example using hydroxyl-functional resins. Polyester resins used to formulate exterior-durable powder coatings typically have an acid value (AV) of 25-40.
33 AV polyester: 56,100/33 = 1700 grams per equivalent
Acrylic resin producers typically include the epoxide equivalent weight (EEW) in their product literature.
33 AV polyester: 1700 / (1700 + 535) = 0.76
GMA acrylic: 535 / (1700 + 535) = 0.24
33 AV polyester | 76.06 |
GMA acrylic | 23.94 |
Total | 100 |
To produce a semi-gloss finish using this method, a proportion of polyester cured with GMA can be combined with a high gloss approach such as polyester reacted with HAA. For a 33 acid value polyester, it is recommended to cure with a ratio of 95 parts polyester to 5 parts HAA.
33 AV polyester: 1700 / (1700 + 535) = 0.76
0.76 x 50 = 38.03 parts per 100 total
GMA Acrylic: 535 / (1700 + 535) = 0.24
0.24 x 50 = 11.97 parts per 100 total
33 AV polyester: 0.95 x 50 = 47.5
HAA: 0.05 x 50 = 2.5
The same polyester resin is used for each fraction, so combined together the binder portion of the formula would be as follows:
33 AV polyester | 85.53 |
GMA acrylic | 11.97 |
HAA | 2.50 |
Total | 100 |
The target gloss can be achieved by modifying the ratio of the polyester/GMA acrylic portion to the polyester/HAA component.
Conclusion
In a market that demands coating finishes of all gloss levels and appearances, the powder coating formulator’s toolbox includes a number of techniques to achieve the desired appearance. For some applications, like a military coating requiring a dead matte finish, multiple approaches can be combined in a formulation to drive the gloss as low as it can go. Understanding these gloss-control methods is crucial to meeting the aesthetic demands of any end-use application.
To learn more, contact the author at nbiller@chemquest.com or visit https://chemquest.com/cqpcr.
Read in CoatingsTech.