Table of Contents
The paint and coatings industry, like many others, faces significant environmental challenges. Amidst these challenges, however, lies an opportunity for transformation toward sustainability. The topic of sustainability encompasses all aspects of our lives. We are flooded with messages about microplastics in the ocean, lawsuits over environmental pollution, detergent “sheets” that reduce waste, and electric cars that eliminate the use of petroleum, to name but a few.
In short, human stewardship of the Earth is undergoing a metamorphosis—and for very good reasons. The planet is getting hotter, and the situation is getting worse. How did we get here, and how can the paint industry, whose products literally cover the Earth, reengineer its products and processes toward a more sustainable future?
Framing the Problem
In 1896, Savante Arrhenius was the first to use the principles of physical chemistry to estimate the extent to which increases in atmospheric carbon dioxide are responsible for the Earth’s increasing surface temperature. He discovered that the warming effects of atmospheric carbon dioxide and water vapor prevent heat flow from the Earth’s atmosphere and offset the cooling effect of the same gases as they radiate heat through the atmosphere into space.
These calculations led him to conclude that human-caused CO2 emissions, from fossil-fuel burning and other combustion processes, are large enough to cause global warming. This phenomenon is known as the greenhouse effect, and the work of Arrhenius (and others) created the foundation of modern climate science.[1]
NASA has measured the CO2 levels in core ice samples from many millennia until now. This analysis shows that it was only at the onset of the industrial revolution and the burning of coal for fuel that the levels began to rise significantly (see Figure 1).
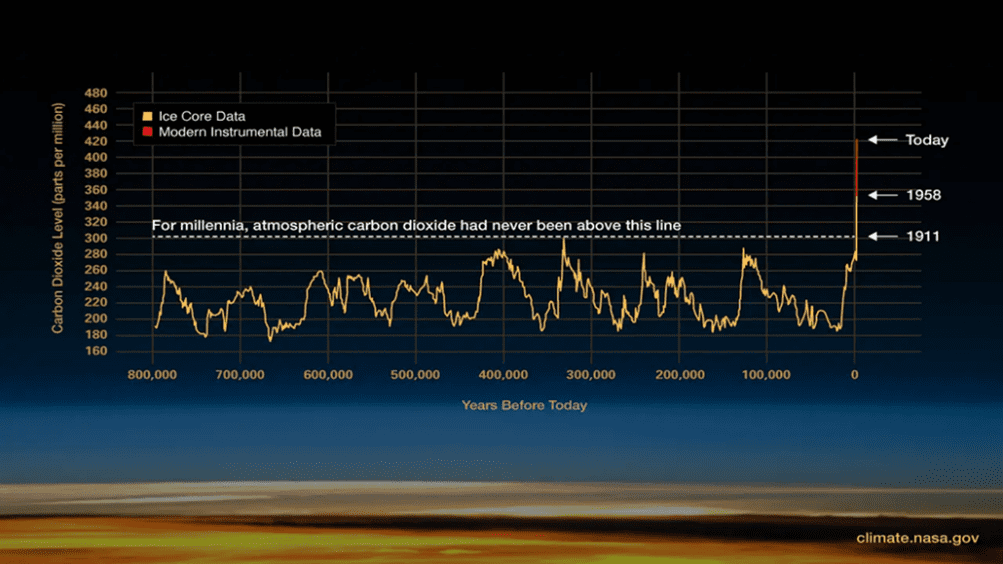
While ocean water serves to buffer the atmosphere by trapping about 91% of the excess heat from greenhouse gases and 31% of human emissions of carbon dioxide, this capacity is severely diminished as ocean temperature measurements rise over time. Warmer oceans result in sea-level rise, iceshelf melting, intensified storms, tropical cyclones, and marine heatwaves.[2]
Thus, global ambient temperatures have been rising every year; according to the World Meteorological Organization, 2023 was the hottest year on record. Trend lines indicate this will continue until we can lower global greenhouse gas (GHG) emissions significantly.[3]
The World Responds
The United Nations (UN) Sustainable Development Goals and the European Green Deal aim to achieve a climate-neutral, pollution-free, sustainable, circular, and inclusive economy by 2050. Major elements of the Green Deal with direct impact on the chemical industry include:
- The European Climate Law
- The New Circular Economy Action Plan
- The Zero Pollution Ambition Pillar
These programs support the Chemicals Strategy for Sustainability and the related Safe and Sustainable-by-Design approach for product development.[4]
In the U.S., the Department of Energy has developed a roadmap known as the Pillars of Decarbonization.[5] The roadmap identifies technological pillars to significantly reduce CO2 emissions, with the goal of 100% elimination, including:
- Efficiency energy—A foundational, crosscutting decarbonization strategy; reducing the energy consumption of the industrial sector is a must
- Industrial electrification—Transitioning industry from combustion fuels to electric power
- Low-carbon fuels—Substitution of low-carbon fuels, feedstocks, and energy sources such as hydrogen, biofuels, or solar thermal power can further reduce combustion-associated GHG emissions for industrial processes
- Carbon capture, utilization, and storage (CCUS)—Multi-component strategy for mitigating hard-to-abate emissions sources; involves capturing generated CO2 before it can enter the atmosphere, utilizing captured CO2 wherever possible, and storing captured CO2 long-term
These initiatives have created the decarbonization market, which currently has an estimated global worth of $2 trillion. The market encompasses the activities associated with the creation of a circular bioeconomy in oil and gas, energy and utility, agriculture, government, automotive and transportation, aerospace and defense, and manufacturing.[6]
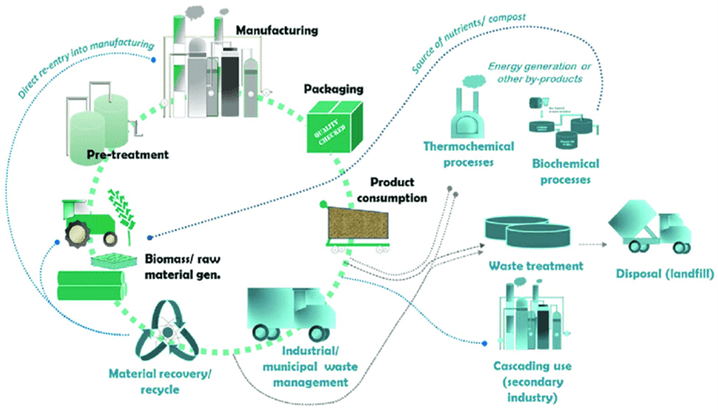
Tracking global decarbonization has become a major activity within businesses, requiring expanded resources and budgets to hire sustainability and carbon managers. The U.S. Securities and Exchange Commission (SEC) requires tracking and reporting on the sustainability efforts of public corporations to disclose climate-related risks for the investment community.[7] In addition, federal and state environmental, social and governance (ESG) laws and guidelines have become essential elements in corporate reports, as growing stakeholder and investor pressures mean that ESG reporting has become a business priority.
Sustainability in the Coatings Industry
Because paint is everywhere, the paint and coatings industry has a tremendous opportunity to implement sustainable and innovative solutions that minimize its environmental footprint. Key opportunities for improvement include:
- Raw material choices
- Improving manufacturing processes
- Longer coating durability and higher performance
- Eliminating materials of concern
- Recycling paint
Raw Materials
Achieving success in a bioeconomy depends on moving from a hydrocarbon, primarily petroleum-based feedstock to a carbohydrate-based feedstock that has a low carbon footprint, as well as replacing solvent carriers with water. Since the early 1980s, the volatile organic content (VOC) of architectural paints has been regulated downward to less the 50g/l of product.
The South Coast Air Quality Management District (SCAQMD) in California has imposed the most stringent VOC reduction rules. According to the organization’s tracking data, there has been a 40% reduction in VOC emissions since 2008.[8]
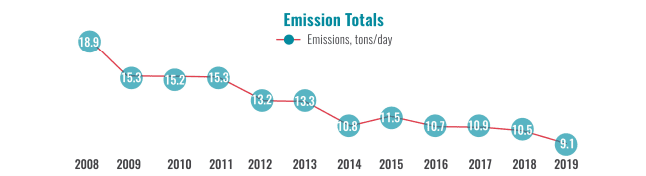
Bio-based raw material equivalents are becoming readily available for use in paint and coating formulas and can be found in all the major coatings categories, including additives, resins, solvents, monomers and oligomers, and pigments. Multiple feedstocks are used to produce these raw material equivalents, such as:
- Lignocellulose (wood)
- Starch (potato, wheat, corn)
- Green biomass (grasses)
- Sugar (beets, cane)
- Organic waste
- Seed and algal oils
Online resources from coating raw material suppliers and formulation websites[9] are excellent starting points for locating bio-based offsets to coating ingredients.
Following testing and performance verification, certifications from third-party organizations (e.g., Green Seal) can verify that low/no carbon content products meet specific standards for performance, health, and sustainability. While rigorous, this type of certification can help qualify products for use in LEED-certified buildings (Leadership in Energy and Environmental Design) as specified by the U.S. Green Building Council.
Manufacturing Processes
New manufacturing technologies that reduce process steps and materials usage can reduce the energy embedded in manufacturing processes. Greater energy efficiency and process optimization through faster mixing and dispersion can improve yields and reduce cycle times.
Examples include using variable-frequency drives on motors that power fans and reducing the use of distillation processes by implementing more efficient solvent recovery systems. Using electricity from renewable sources, implementing water reuse programs, and recycling waste to achieve zero output all serve to increase sustainability goals.
Higher Performance and Transfer Efficiency
Extending the lifetime of a paint, particularly on high-value assets, decreases GHG by increasing the time to repaint. For industrial coatings, this means better corrosion and crack resistance, adhesion, weather resistance, cleanability, and color fastness.
VOC reduction has made many of these properties more difficult to achieve, particularly for industrial coatings that may need more time for complete cure. That said, the industry continues to strive for higher performance in architectural paints by providing better hide in one application coat, self-cleaning properties, dirt pick-up and scratch and mar resistance, as well as resistance to repeated scrubbing and cleaning. Increased use of UV- and radiation-cure technologies, as well as powder coatings, can provide higher performance in factory-applied products and reduce energy consumption by eliminating the need for heat tunnels.
Maximizing paint transfer efficiency also reduces GHG emissions. Using electrostatic spray technology drastically increases transfer efficiency with little waste. Others are exploring the use of inkjet printing technology to the surface, delivering all colors needed at one time with nearly 100% efficiency.
Boeing has designed several precision application methods using piezoelectric paint jet robots that deliver drop-on-demand paint with high resolution. Because the paint is applied in thin coats, the airplane achieves a weight reduction that results in fuel savings.
Eliminating Materials of Concern
As previously seen, VOCS have dropped significantly due to global regulatory constraints and the need to reduce GHG emissions. Transitioning to water-based carriers and the use of powder coatings has contributed to this reduction. However, other materials of concern have come under regulatory scrutiny, such as heavy metals, antimicrobials, crosslinking agents, fluorinated compounds, and microplastics.
Raw material suppliers and formulators have worked to find substitutes or create new chemistries to meet product performance specifications. Examples include new bisphenol A substitutes to crosslink epoxies, heavy metal-free marine antifoulant additives that do not kill the surrounding habitat, and alternative technologies that replace fluorosurfactants for dirt and block resistance and reducing surface tension.
So-called forever chemicals like per- and polyfluoroalkyl substances (PFAS) are a group of compounds that have recently come under sharp focus for elimination from use, as some have been associated with severe and persistent health effects. The EPA has created a strategic PFAS roadmap for tracking and eliminating PFAS from the environment.[10]
Proactive paint manufacturers have been actively reformulating products to remove any PFAS-based compounds, though the generation of microplastics has now been associated with paints and coatings.[11] While some studies attribute 58% of microplastics in the ocean as coming from paint binders, research is ongoing and further studies are planned to provide more definitive data.
Recycling Paint
While consumers can recycle shipping containers, plastic buckets, and metal paint containers, it is more difficult to dispose of liquid paint. It is likely that every garage or basement in the U.S. has at least one old, unusable gallon of paint sitting on the shelf. Some local municipalities sponsor days when they will accept these materials and dispose of them as hazardous waste.
Fortunately, the American Coatings Association (ACA) established a product stewardship program called PaintCare®[12] and has initiated programs in multiple states for the collection of unwanted and leftover paint. PaintCare has launched programs in California, Colorado, Connecticut, the District of Columbia, Maine, Minnesota, New York, Rhode Island, Vermont, Washington, Illinois, and Maryland.
To date, the program has collected about 70 MM gallons of paint. Some might call this a drop in the bucket, but providing a safe, reliable way to responsibly dispose of paint represents leadership in sustainability. Hopefully, this program will expand to all 50 states.
Climate-Driven Needs for Innovative Coatings
Because the world is getting hotter, implications for the paint and coatings industry call for the creation of new technologies and products that address the new normal. These include:
- Optimized application of paints at higher ambient temperatures
VOCs have been regulated to below 50 g/l, causing short open time for application. It is not recommended to apply paint when temperatures are elevated. Environmentally adaptive technologies are needed to increase the application working time to assist in better spread rates and coverage, especially in areas where the ambient temperatures remain high for extended periods of time. - Better water resistance/repellency
Products applied in heavy storm/hurricane-prone areas need to provide increased water resistance that is above current levels to provide better substrate protection, especially during periods of wind-driven rain. - Increased mold and mildew resistance
High moisture conditions exist after major storms and floods, accelerating mold and mildew growth. Wall paints and other coatings need to be reinforced with environmentally safe antimicrobial additives for better substrate protection and to help maintain a healthy environment. - Fire-resistant coatings
The frequency of wildfires is increasing due to lack of rain, even in normally temperate climates. Fire-resistant additives in paints and roof treatments could add safety benefits to the performance if they help increase the time for escape from dangerous fires by slowing the rate at which flames spread. These products typically pass ASTM E-84, a test developed by the American Society of Testing and Materials (ASTM) to provide comparative measurements of surface-level flame spread and smoke density. - Coatings that reduce surface temperature
Cooling the building envelope by applying coatings with high solar reflectance can reduce the cooling demand of the built environment. Lowering the cooling demand results in lower energy costs, reducing the stress on the electrical grid. Coatings with >98% solar reflectance and high thermal emittance can significantly lower the internal temperatures of a building.
Final Thoughts
Paints and coatings represent a mature industry and, in many respects, has been operating with established manufacturing methods for decades. As the world comes to grips on how best to address increasing GHG emissions and regulatory, investor, and consumer pressures have increased, the industry has been increasingly reassessing its environmental carbon footprint and developing strategies to reduce it. The challenge of climate change presents serious risks for businesses that do not act, but addressing these challenges aggressively can provide significant opportunities for companies to establish themselves as leaders in sustainability.
To learn more, reach out to the author at vscarborough@chemquest.com.
References
- “On the Influence of Carbonic Acid in the Air upon the Temperature of the Ground,” London, Edinburgh, and Dublin Philosophical Magazine and Journal of Science (fifth series), vol 41, 237–275, April 1896.
- Li, Z., England, M.H., and Groeskamp, S.,“Recent acceleration in global ocean heat accumulation by mode and intermediate waters,” Nat Comm 14, 6888, 2023.
- “Climate change indicators reached record levels in 2023: WMO,” www.wmo.int/news/media-centre/climate-change-indicators-reached-record-levels-2023.
- “EU Commission unveils ‘European Green Deal’: The key points,” www.euravtiv.com, December 11, 2019.
- “Industrial Decarbonization Roadmap,” Department of Energy, DOE EE-2635, September 2022.
- Kadambari Lokesh, et. al, “Bridging the Gaps for a ‘Circular’ Bioeconomy: Selection Criteria, Bio-Based Value Chain and Stakeholder Mapping,” Sustainability, 10(6), 1695, 2018.
- “SEC Proposes Rules to Enhance and Standardize Climate-Related Disclosures for Investors,” www.sec.gov/news/press-release/2022-46.
- “Sustainability Report 2022,” American Coatings Association, Washington, D.C.
- Such as www.ulprospector.com, www.knowde.com, www.coatings.specialchem.com.
- “PFAS Strategic Roadmap: EPA’s Commitment to Action 2021-2024,” Environmental Protection Agency, EPA-100-K-21-002, October 2021.
- Fang, C., et. al., “Paint has the Potential to Release Microplastics, Nanoplastics, Inorganic Nanoparticles, and Hybrid Materials,” Environmental Sciences Europe, 36, 17, 2024.
- “ACA and PaintCare: Advancing a Post-Consumer Paint Solution,” American Coatings Association, May 2022, www.paintcare.org.
Read in PCI.